
How to Select the Correct Barbed Connector for your Single-Use System
Mechanical hose barb connections consist of three elements: the hose barb, tubing and retention device. The process of bringing all three together to create a secure connection is crucial for maintaining system integrity, preventing leaks and ensuring product safety.
Selecting the correct barbed connector for your single-use system involves taking into account various factors to ensure compatibility and functionality. Outlined below are the key considerations when establishing a secure hose barb connection.
Hose barb
A secure and reliable connection is determined by how well the fitting and tubing work together, so selecting the proper barbed connector is just as important as the choice of tubing and can ensure product performance, increase ease of use, and add functionality to your product designs.
Hose barbs are available in many different styles including straight, elbow, cross, Y- and T-connectors, and are typically described by the nominal inner diameter (ID) of the tubing they are intended to be inserted into. This description should not be interpreted as a guarantee of performance of the connection with any specific sized tubing. There are no consensus standards for barb dimensions to fit tubing IDs. In many cases, a barb may be used with different ID tubing than described.
The choice of barb depends on several factors including the material, elasticity, durometer and dimensions of the tubing; the use and selection of a retention device; the ease of assembly; the intended use; and required pressure and pull-off resistance of the tube-to-barb connection. For general use in a laboratory setting, ease of assembly and convenience may be the greatest influence when making a decision. For SUS where integrity is more imperative, the shelf life, security and reliability of the connection may drive the decision.
The requirements for the connection should be assessed and appropriate technical due diligence used to ensure connection performance is aligned to the user’s requirements.
(Refer to ASME BPE – 2022, Chapter 9, Section SJ-2 for specific requirements for hose barb connections used in SUS for bioprocessing.)
Other factors that should be considered when selecting a hose barb connector are material compatibility with the intended fluid or application, sterilization compatibility and regulatory requirements such as biocompatibility.
Qosina offers a selection of single-use barbed tube-to-tube connectors in the styles shown below:
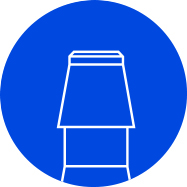
A
- Nominal size range: 1/16”–1/4”
- 50% oversized barb
- Oversized barb stem
- No parting line on barb
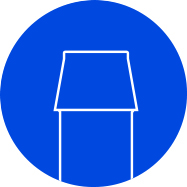
B
- Nominal size range: 1/8” – 1”
- 18% to 34% oversized barb
- Oversized straight barb stem
- No parting line on barb
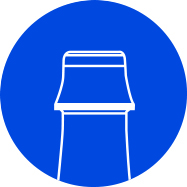
C
- Nominal size range: 1/16” – 1”
- 12% to 57% oversized barb
- Tapered barb stem
- No parting line on barb
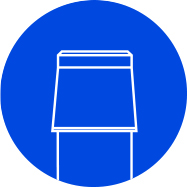
D
- Nominal size range: 1/8” – 1”
- 10% to 25% oversized barb
- Barb stem sized equal to nominal tubing ID
- Anti-rotation ribs on barb stem
- No parting line on barb
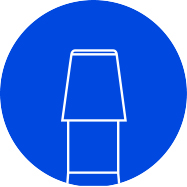
E
- Nominal size range: 1/16” – 1/4”
- 50% to 100% oversized barb
- Oversized barb stem
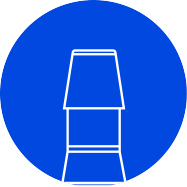
F
- Nominal size range: 1/16” – 3/8”
- 40% to 60% oversized barb
- Oversized barb stem
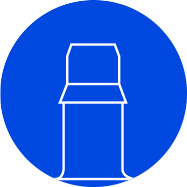
G
- Nominal size range: 1/16”–1/4”
- Straight line feature
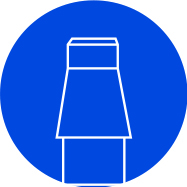
H
- Nominal size range: 1/16” – 1/4”
- 40 to 70% oversized barb
- Extended barb
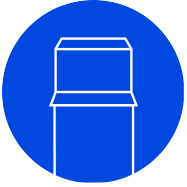
I
- Nominal size range: 1/16” – 1/4”
- 25% oversized barb
- Designed for semi-rigid tubing
Tubing
Choose tubing or hose materials that are compatible with the intended application and provide a secure fit over the barb.
Flexible tubing is available in a variety of materials, dimensions and mechanical properties. Typical materials include platinum-cured silicone, thermoplastic elastomer (TPE) and PVC. Tubing IDs may be available with different wall thicknesses. The elasticity and durometer of the material also influences the ease of assembly and performance of the connection.
Match materials to the application
The choice of tubing is driven by many factors including pumpability, weldability, chemical compatibility and direct experience with the tubing choice. These factors compound the importance of a diverse selection of readily available tubing choices for your single-use application.
The tubing solutions available today all exhibit different levels of flexibility, a factor that plays a large part in how well a connection performs.
In general, the softer the tubing, the more likely that a hose barb type fitting is appropriate for the application. While it is the ID of the tube that largely determines selection of the proper fitting, there are other factors to consider:
-
Pull‐off resistance: When a tube is pulled, it tends to contract and grab more tightly. A particular fitting will therefore exhibit different tensile strength characteristics for different sizes and grades of tubing. If the barb is too sharp and the tubing is very soft, enough pulling and vibration could cut the material and cause leaks and failure. On the other hand, a shallow or rounded barb mated with very stiff tubing may allow a tube to disengage with minimal pulling force.
-
Blow‐off resistance: Spikes in pneumatic or hydraulic pressure tend to make tubes expand, potentially loosening the grip of the barb. For high-pressure applications, the shape and arrangement of barbs and the relative flexibility of the tubing determines how the connection will perform under expansion of the tubing material.
Reduced blow-off and pull-off resistance is more likely if there is a mismatch between barb design and the durometer of the host or tubing. A poor match can cause other problems, too. It can make installation and maintenance much more difficult, and this can lead to leaking.
-
Ease of installation: Shape and placement of barb(s) on fittings combined with tubing flexibility determine the force required to connect the fitting to the tubing. Easing the burden of the installation technician is one issue to consider. More important, if it is too difficult to push tubing onto the fitting, the tubing may not grip properly and open the possibility for leaks and failure.
Reference: Get a Grip! An introduction to hose barbs, Colder Products Company
Hose/tubing inner diameter
Another key component of determining tubing terminations is the accuracy of the inner diameter of tubing. Given the inherent variability in tubing and hose material, it is important to carefully select a fitting or coupling that meets the inside diameter specification of the tubing being used. There are no consensus standards for barb dimensions to fit tubing IDs. In many cases, a barb may be used with different ID tubing than described.
Outside diameter of the barb
The OD of the barb(s) needs to be correlated to the ID of the tube it will be attached to. When designing a connector, the accuracy of the tube's ID, material, tube flexibility and application will be critical. For tighter seals where no retention device will be used, you'll need to increase the OD of the barb(s),but be careful as to not go overboard. If you do, installation could become your biggest bottleneck.
- Sharp vs. rounded edges: Depending on the tube/hose material used, you'll need to use a barb that is just sharp enough to grip/seal the tube, yet round enough as to not cut into the tube.
- Parting line: In making a plastic part, a mold opens and closes as each piece is produced. In this process, a parting line is created: a seam that produces a slight imperfection on the plastic part where the two halves of the mold meet. On the barb of a fitting, a mold parting line invites leaks and system failure. Parting lines are especially prevalent with a poorly molded part or where the manufacturer has skimped on tooling investment or maintenance.
Retention device
Retention devices are generally placed closely behind the barb and are used to improve the connection’s pull-off strength and pressure resistance.
Determine the optimal connection method for your application. Common retention devices include cable ties and Oetiker® clamps. Ensure that the chosen method provides a reliable and leak-free connection.
Cable ties are an inexpensive and easy solution that has been utilized for years. They’re specified by their width, length, breaking strength and color. We should note that cable ties are distributed from industrial suppliers who may not have the controls in place that are required for the bioprocessing industry. Suppliers who choose to use cable ties should consider this in their decision process.
Oetiker® clamps are specified by their width and diameter range, with a suggested compression of the tubing material under the clamp. Most Oetiker® clamp sizes are available in a degreased format, improving their suitability for assembly in a cleanroom.
Pressure and temperature ratings
Verify that the hose barb and associated components can withstand the pressure and temperature conditions of the application. Ensure that the selected components meet or exceed the operating parameters to prevent failure and leaks.
Testing and validation
Perform testing and validation of the selected barbed connector within the context of your specific application to ensure it meets the performance requirements and maintains integrity.
Regulatory compliance
Ensure that the hose barb connection complies with industry-specific regulations and standards, especially in medical device and bioprocessing applications. Adherence to standards is essential for regulatory approval and ensuring product safety.
Conclusion
Hose barbs are an integral part of today’s fitting and coupling solutions, providing a low cost and effective means for connecting many different types of tubes and hoses. To ensure a safe and secure system, determine how these critical elements work together to provide the best grip and seal for your application.
By considering these factors, you can establish a secure hose barb connection that meets the stringent requirements of the bioprocess and medical device industries. Always follow industry best practices and adhere to relevant standards and regulations.